Process Description
The filter oil is filtered at low temperature, and the temperature is lowered to 15~20°C to minimize the volatilization loss of fragrance. The new process of filtering, standing and filtering has changed the traditional process of filtering after hydration. Fully filter out the phospholipids that are not easily hydrophilic, so that the content of phospholipids in the oil can be reduced to a minimum, so as to improve the stability of the storage period.
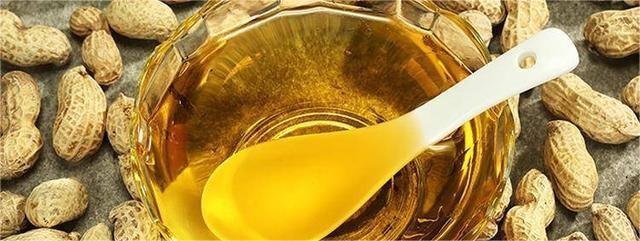
(1) The first filter: Crude crude oil is pumped into the filter for filtration after initial slag removal in the oil tank, and the obtained primary filtered oil is pumped to the cooling pan, and after cooling to a certain temperature, it is pumped into the oil tank with cooling coils and refrigerated. .
(2) The second filter: The primary filtered oil is left to stand to further combine the easier-to-combine water-containing phospholipids, and the secondary filtration with strong water absorption separates the part of the phospholipids that have been polymerized to achieve the effect of filtration and polishing. It makes the oil have excellent transparency, improves the sensory index, and further improves the stability of the storage period. The filtered oil is left to stand for 3 days, and the plate and frame filter is used for secondary filtration to obtain the finished natural flavor peanut oil.
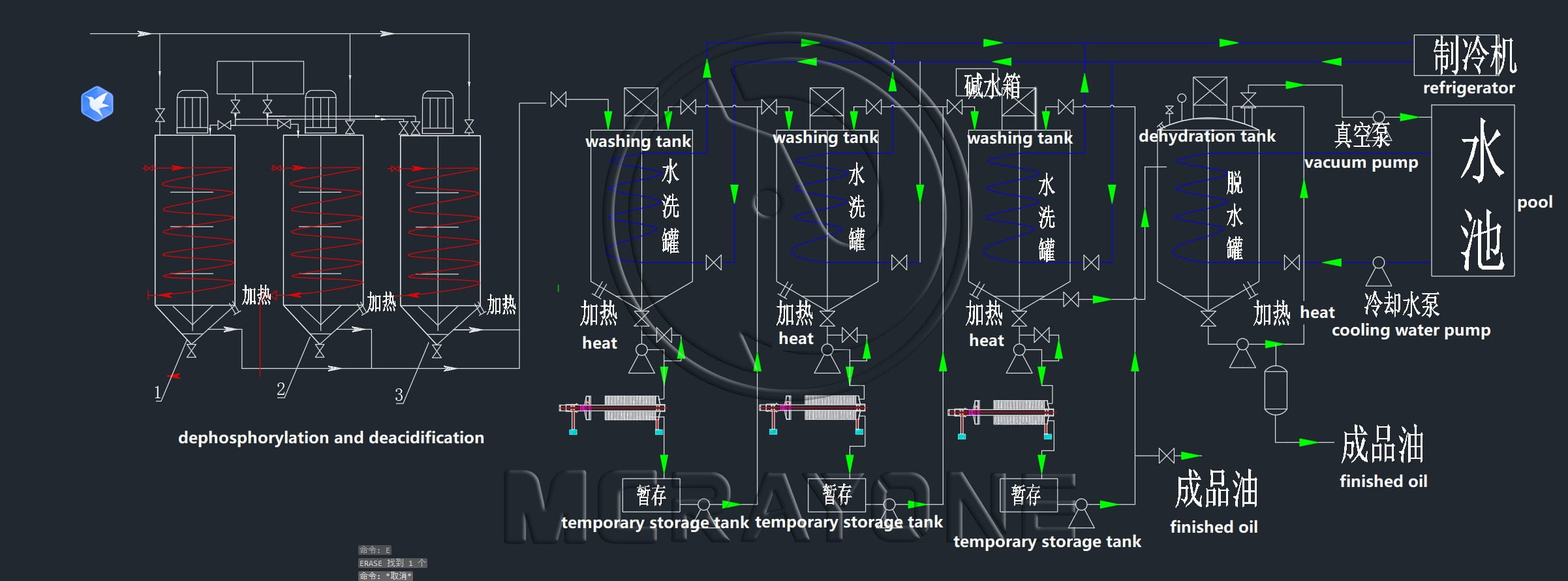
Peanut oil produced by ordinary processes needs to be refined.
The basic process is as follows
- Transportation of peanut oil.
Before the filtered crude oil is pumped into the refining tank, check whether the pipeline valve is normal, and immediately close the oil inlet valve after each tank is delivered. The crude peanut oil to be refined in the oil tank must first remove the foam on the oil surface to make the oil surface smooth, and let it stand for an appropriate time (not less than 15 minutes), so that there is no foam in the oil. Adjust the crude oil temperature to 25-35°C.
When the oil surface of the crude oil is smooth and the temperature is stable at 25--35°C, start the agitator to start stirring, open the valve of the alkali tank at the same time, and put in the lye. The time for adding lye is generally about 15 minutes. After the lye is discharged, continue to stir quickly until the oil and soap particles are clearly separated. When the oil and soapstock are clearly separated, change to slow stirring, open the heating steam valve, stop stirring when the temperature of the oil rises to 60°C, and close the steam valve to allow it to cool and precipitate by itself. After checking that the pipeline of the oil delivery valve is normal, pump the oil into the water washing tank.

Heat the oil pumped into the water washing tank, and at the same time start the agitator and add hot water to keep the oil temperature at 80--85 °C. When the water is added, stop heating, continue to stir for 15 minutes, settle for 2 hours (for the first time), open the drain valve at the bottom of the washing tank, and drain about 3/4 of the washing water. Then close the drain valve, open the valve leading to the oil-water separation tank, and slowly put the remaining oil-water mixture.
Continue to wash the oil with water according to the above method until the washing water is completely clear, and the precipitation time for the second washing is 1.5 hours.
Pump the washed oil into the vacuum dehydration tank, open the steam valve at the same time, start the vacuum pump and agitator, adjust the cooling water of the condenser, and start the circulating oil pump to accelerate the oil circulation in the vacuum dehydration tank. The vacuum degree of the vacuum dehydration tank is kept above 0.0867MPa. The dehydration time is about 1-3 hours. The dehydrated oil should be sampled and inspected. If the dehydration is found to be insufficient, the dehydration must be continued.
After the dehydration is completed, stop the vacuum pump, open the air valve, and slowly put in air. Then the delivery oil is cooled to 25--30°C through the cooling pipe and flows into the sedimentation tank for filtration.
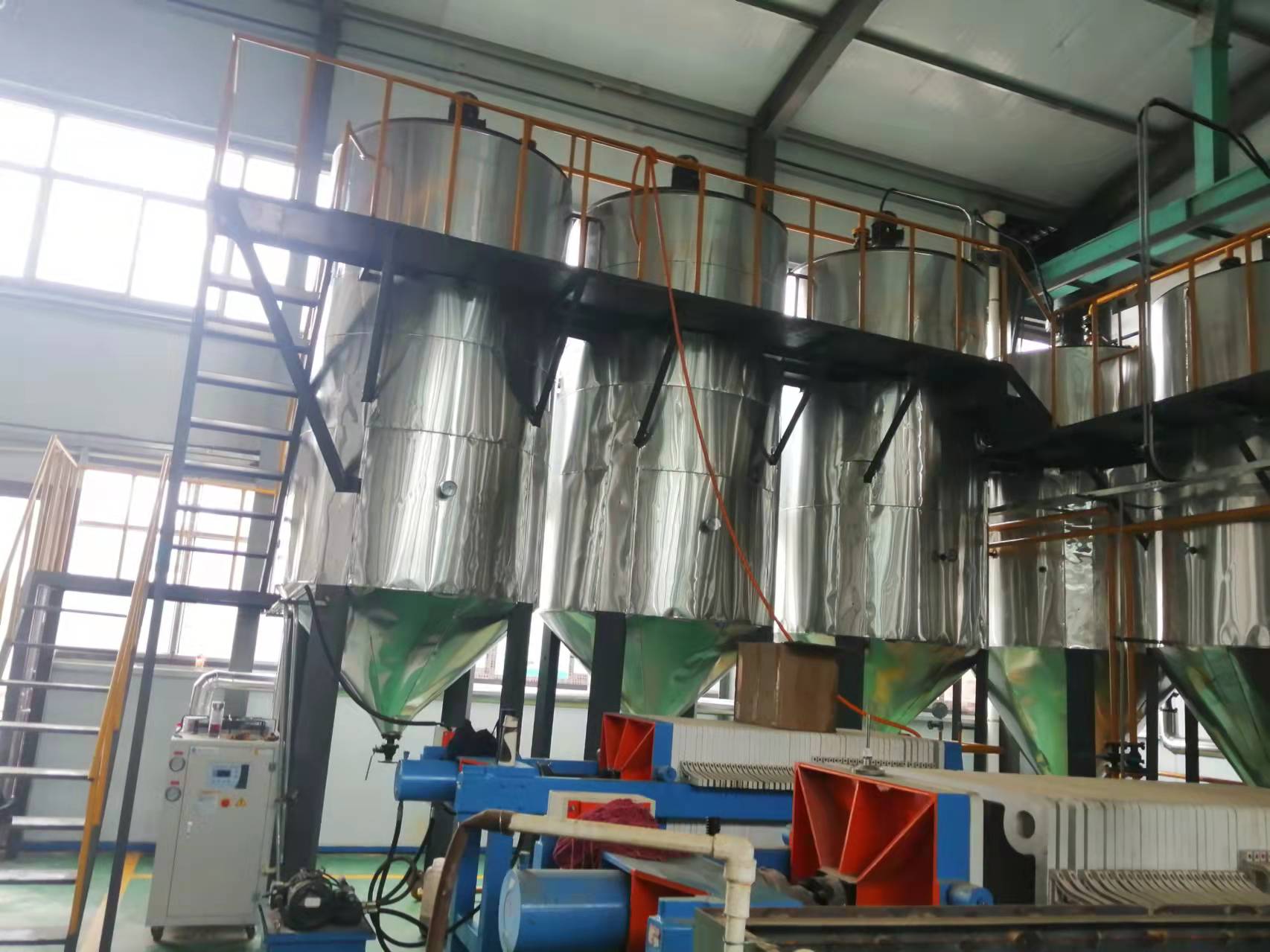
Check that the oil temperature must be below 30°C. After the oil is filtered, stop the oil filter pump and close the valve, gently open the filter plate to let the internal oil flow into the oil pan, and then remove the filter residue on the filter cloth. Check the condition of the filter cloth and prepare for replacement or washing. The residual oil of the filter cloth should be separated and recovered by the oil-water separator.
Use the oil-water separation tank to separate the recovered oil and then refine it again.
Mainly to remove waxy substances contained in oil.
After refining, it is pumped into storage tanks or filled for storage.
Name
|
Specification
|
Peanut Sheller
|
Capacity:customized according to customer needs
2-25 tons have been customized in the past
Material: carbon steel/stainless steel
Function: Dephosphorylation, deacidification, dehydration, dewaxing
|
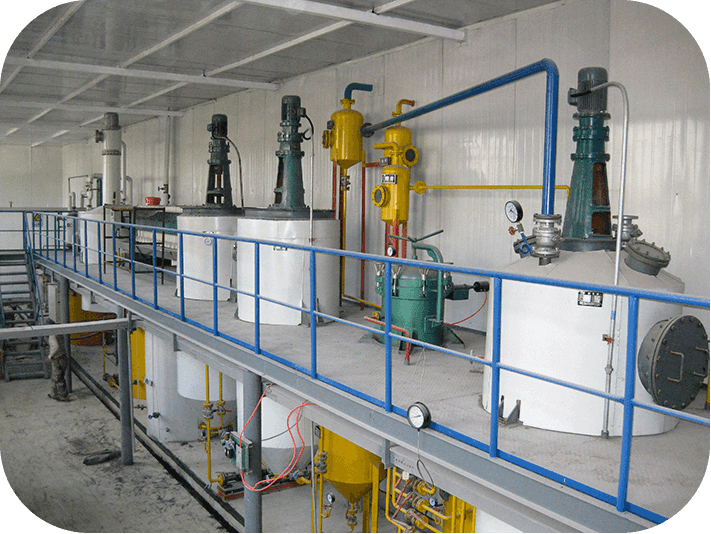