Cottonseed Fleece and Pressing Oil Production
Cottonseed contains gossypol, and high-moisture steaming or puffing is required in the pretreatment process to reduce the content of gossypol in the crude oil and improve the quality of the cottonseed oil. However, gossypol in cottonseed meal, crude oil and cake produced by traditional oil production methods contain gossypol, which affects the feed value of the cake. The cake needs to be detoxified before it can be used as feed. This process well solves the problem of detoxification of cottonseed meal.
Cottonseed contains 39-52% shell and 48-61% kernel. The shell contains 0.3-1% oil. Cottonseed contains 30-35% oil and 35-38% protein. Cottonseed contains 0.8-1.3% gossypol. The traditional cottonseed oil production process is pre-pressing leaching method or pressing method. Since cottonseed has a high hull content and contains gossypol, it is necessary to peel off the hulls and use high-moisture steaming and frying in the pretreatment process to reduce the content of gossypol in cottonseed oil.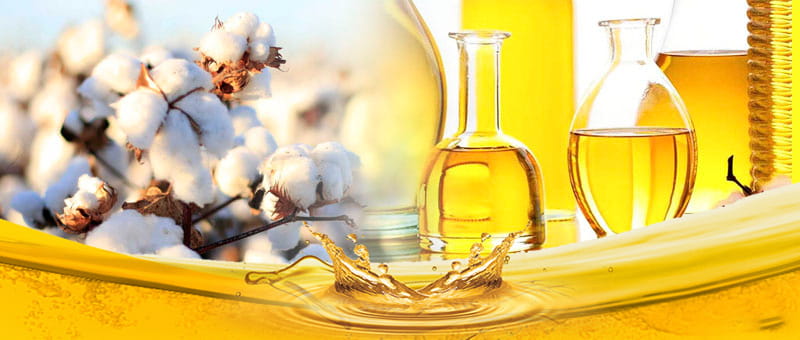
Oil Making Process:
Cottonseed→Cleaning→Hulling→Kernel Shell Separation→Germ Flaking→Expansion/Steaming→Pressing→Crude Oil/Cake
Explanation: A small amount of gossypol remaining in cottonseed crude oil can be removed during the deacidification process of oil alkali refining without affecting the quality of the final oil product. The protein content of dehulled cottonseed meal is 50-60%, and the quality of cottonseed protein is similar to that of soybean protein. However, due to the toxicity of residual gossypol in cottonseed meal, it cannot be directly used as feed. Special detoxification treatment.
Cleaning: Cotton seeds are separated by air and magnetic to remove impurities, and then evenly fed into the sheller by quantitative feeder.
Shelling: In the process of shelling, special attention should be paid to the uniform particle size of the cotton kernel after shelling, so as to reduce the powder degree of shelling. After the kernel shell is separated, it is required that the shell content in the kernel should not exceed 10%.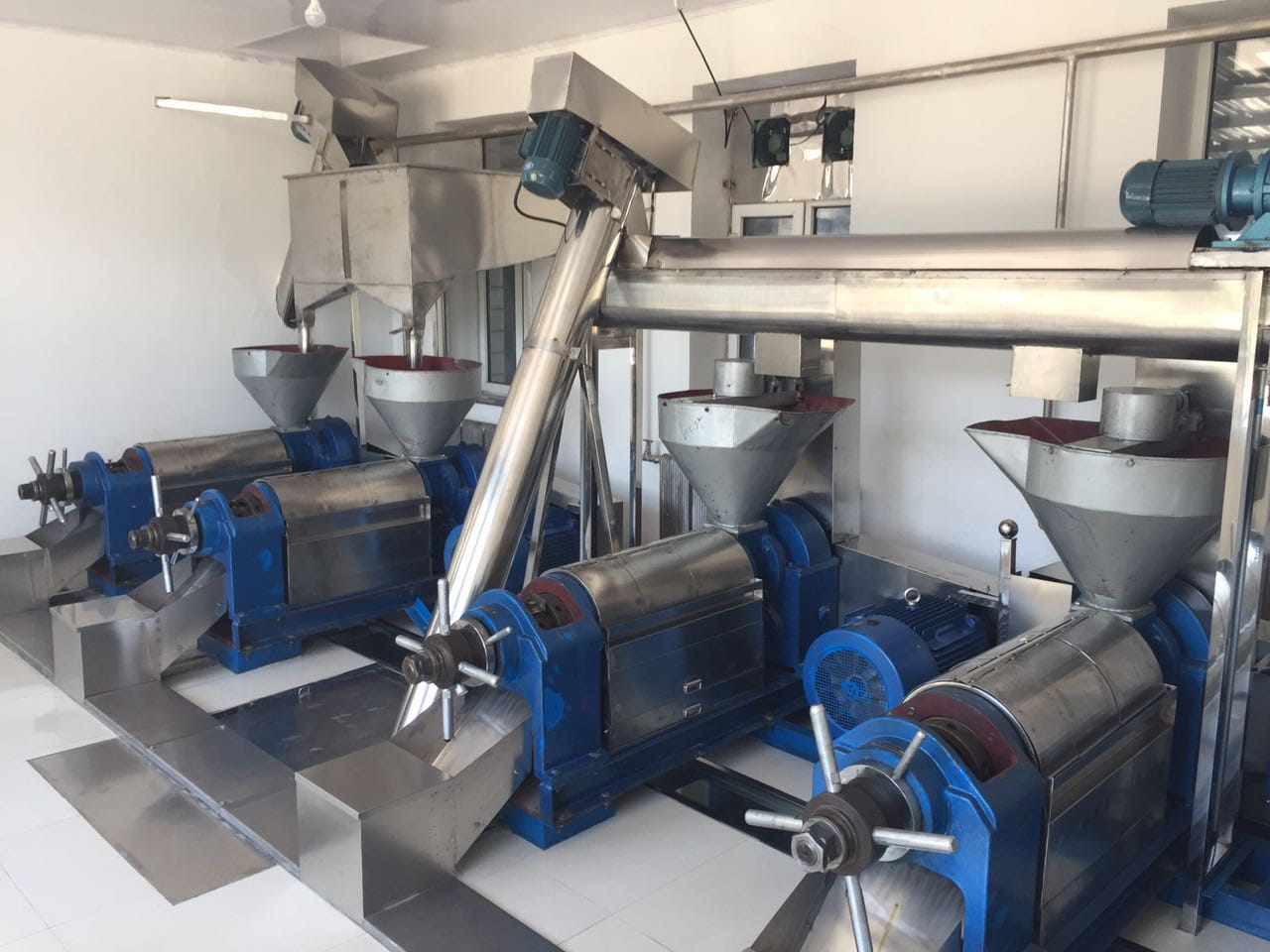
The effect of steaming or puffing will directly affect the working status of the pressing process and the quality of the final product. The mastery of its softening temperature, time and moisture is very important. The softening of cotton kernels generally uses a three-layer or four-layer vertical steamer. It is also possible to use an extruder for instant expansion, which is beneficial to the removal of gossypol in the subsequent process.
In the Flaking process, the thickness of the flakes after flaking should not exceed 0.5mm, the flakes should be solid, and the powder degree should be small. The flakes must be dried, and then cold pressed by a press to form them.
Pressing: The pressing efficiency of the oil press and the stability of the equipment are the key to the oil pressing process. The oil press produced by our factory has the characteristics of large output, low cake residue and good quality cake.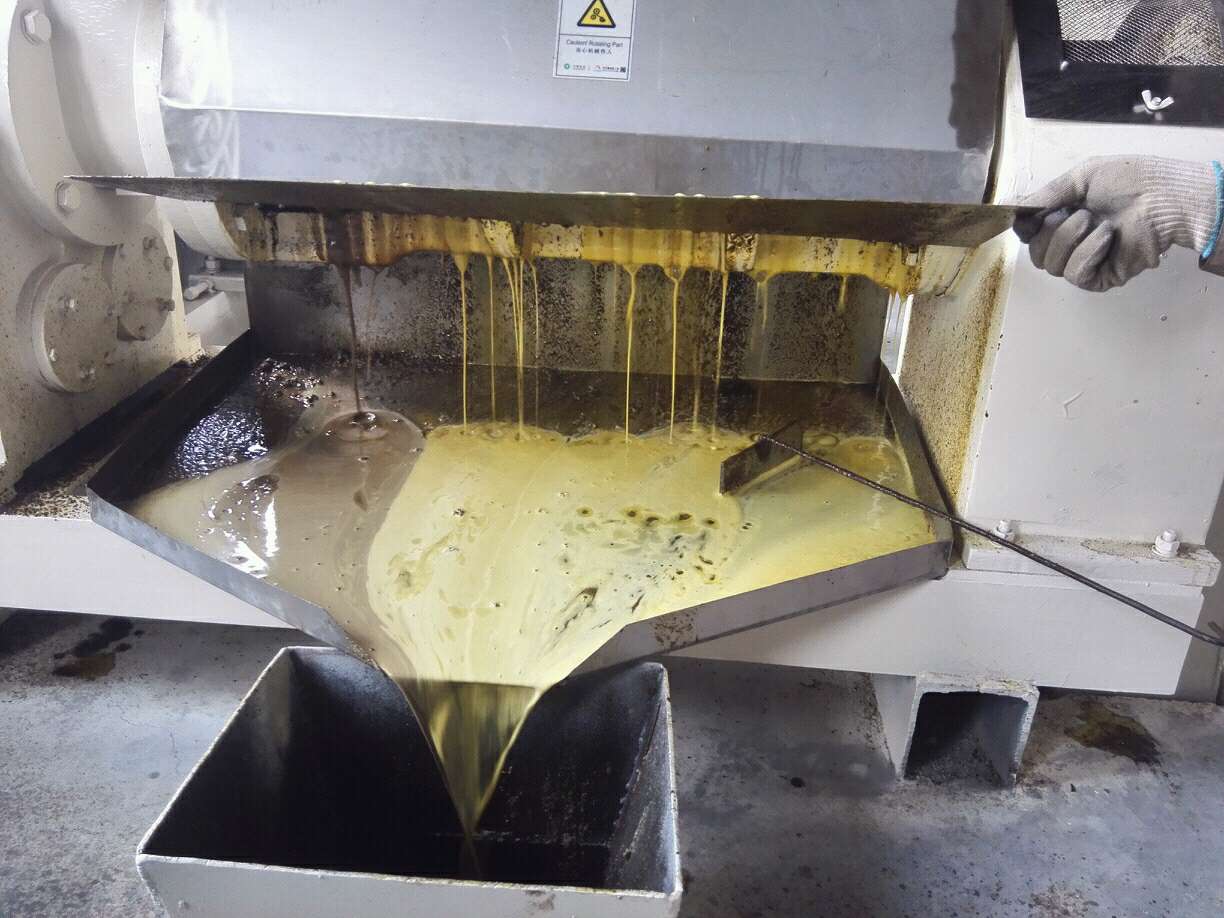
Refining of Cottonseed Oil
1.Degumming and hydration of cottonseed oil
The colloidal impurities in crude oil are mainly phosphorus. The presence of colloids such as phospholipids not only reduces the quality of oil, but also promotes the transitional emulsification between oil and lye in the process of alkali refining and deacidification, increasing the difficulty of separation of saponins and aggravating the loss of neutral oil. Therefore, it should be removed first.
2.Deacidification of cottonseed oil
Oil deacidification is mainly to remove free fatty acids in crude oil, as well as a small amount of colloid, pigment and trace metal substances in oil. Deacidification operation is one of the important factors that directly affect the oil yield and quality of oil refining. The most widely used in industrial production is the alkali refining deacidification method.
3.Decolorization of cottonseed oil
The color of the oil and some other impurities must be decolorized to meet the product quality standards. At the same time, it provides more favorable conditions for deodorization and refining. Decolorization should meet the final color index of the product; remove relevant pigments and quantitative metals; further remove trace saponins, phospholipids and other colloidal impurities and some odorous substances remaining in oil; remove polycyclic aromatic hydrocarbons and residual pesticides; reduce oil quality oxidation value.
4.Cottonseed oil deodorization
The purpose of oil deodorization is to remove odor-causing substances and other volatile substances in oil, improve the smell and color of oil, and improve the stability of oil quality. Odor peculiar to fats and oils, odors generated during decolorization, clam odors caused by oxidation of fats and oils, etc. In the deodorization stage, it is required to directly spray steam into steam distillation at high temperature in vacuum to remove these unwanted odors.
Complete Oil Refinery
|
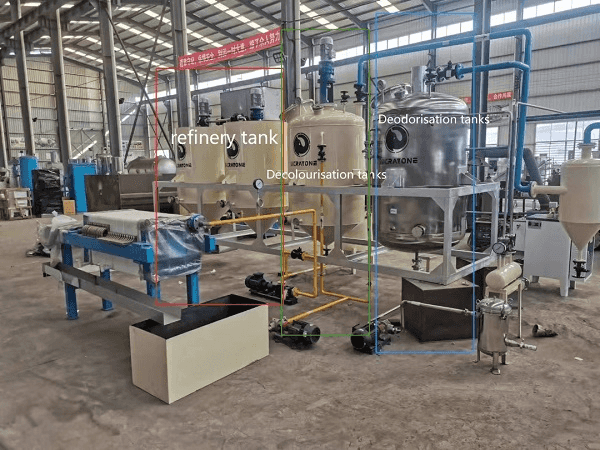
|
Capacity:0.5TPD
200kg*4 tanks
Heating: Electricity 120kw
|
Capacity:1TPD
500kg*4 tanks
Heating: Electricity 120kw
|
Capacity:2TPD
1T*4 tanks
Heating: Electricity 170kw
|
Capacity:3TPD
1.5T*4 tanks
Heating: Electricity 225kw
|
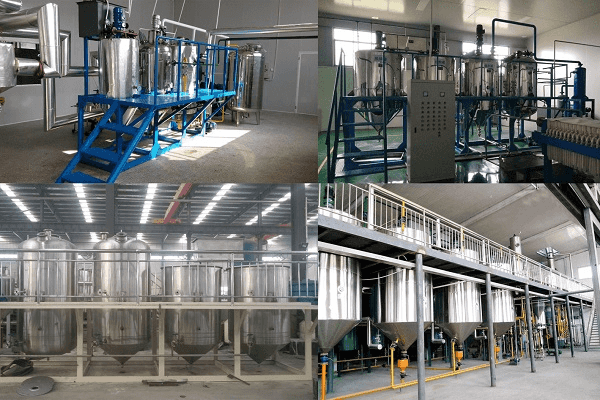
Production Line List Example
No.
|
Equipment
|
Model
|
Specification
|
Picture
|
1
|
Cottonseed Delinting Machine
|
AY-40
|
Number of saw blades: 40 pieces
Size: 1300*1150*1200mm
Weight: 450kg
Capacity:700kg/h
Power: 7.5kw
|
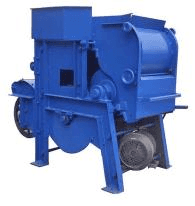
|
2
|
Bucket
Elevator
Optional
|
|
Power:0.75kw
Design according to the final drawings, plant requirements, etc
Material: carbon steel
|
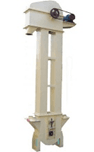
|
3
|
Disc Sheller
|
AY-71
|
Capacity: 35T/D
Power: 18.5kw
Weight: 1100kg
Size: 1820*940*1382mm
|
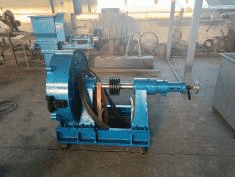
|
4
|
Round Sieve
|
AY-50
|
Capacity: 15-20t/d
|
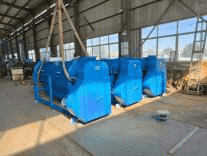
|
5
|
Conveyor
Optional
|
TS160
|
Capacity:2.1T/H
Power: 1.5kw
Material:Carbon steel
Size: 2.56*0.35*0.67m
Weight:150kg
|
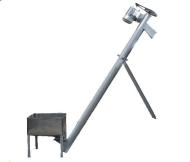
|
6
|
Oil Press
|
ZX130
|
Speed: 450-500 kg/h
Capacity: 10-12 T/ 24hrs
Power: 18.5 kw-6P
Size: 2010*800*1380mm
Weight: 820 kg
|
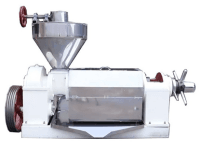
|
7
|
Plate Frame Oil Filter
|
YLB307
|
Filter Area: 3m2
Capacity: 120-180 kg/h
Plate Size: 355*355mm
Plate Quantity: 13 pcs
Power: 1.5 kw-4P
Size: 1270*570*640mm
Weight: 430 kg
|
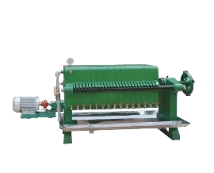
|
8
|
Simple refining
|
3TD
|
Tanks number:4
Function:dephosphorylation deacidification dehydration
Material:carbon steel
|
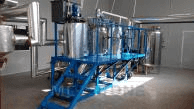
|
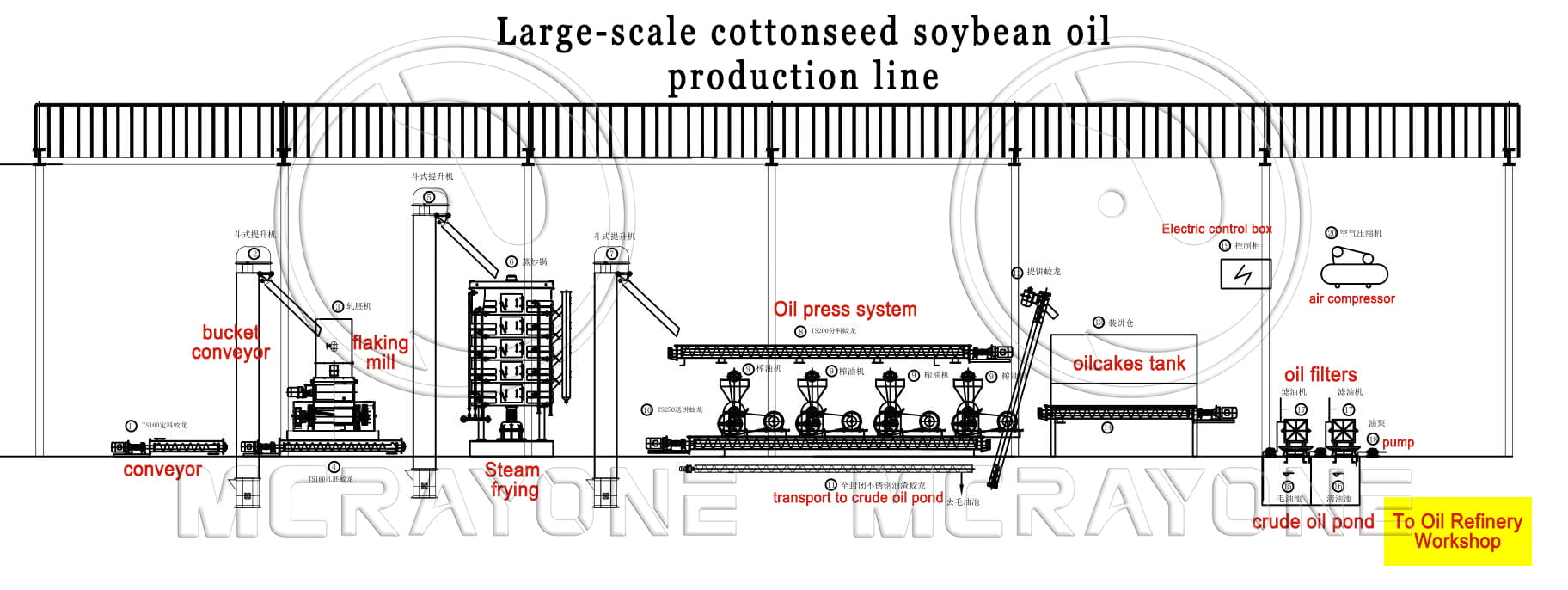